GulfCoat® Contractor Series is the complete solution for the HVAC/R Professional
Offer one of the best corrosion protection solutions available with GulfCoat® Corrosion Coatings – a unique and proprietary coating process that provides air conditioning and refrigeration systems with one of the highest levels of protection to withstand harsh, corrosive environments and provide long-term evaporator and condenser coil protection for longer service life, long-term efficiency, and lower total cost of ownership.
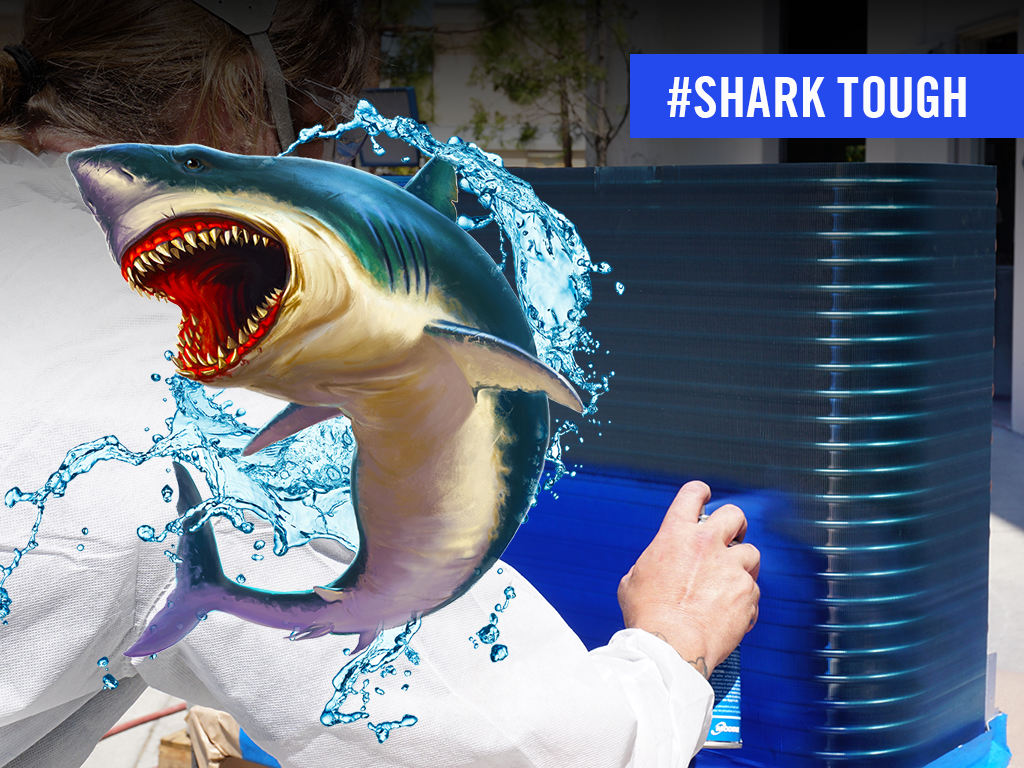
GulfCoat® is Test Proven
The Contractor Series offers a full line of easy to apply products to protect HVAC/R equipment and components. The protective coatings help safeguard against corrosive environmental factors encountered in coastal, industrial, agricultural and high air pollution areas to maximize system life and make cleaning and maintenance easier.
At Modine we have the most stringent quality standards, and our products pass the most arduous industry tests to ensure their top performing in the field.
A corrosion protected HVAC/R system can provide energy cost savings and extend the equipment’s operating life in any environment but is particularly beneficial in coastal regions where air borne salt spray is common. Additionally, corrosion is an issue in arid desert environments, or around heavily industrialized areas. Simply put, anywhere corrosive environments are present, applying GulfCoat® Contractor Series is easy to apply solution for longer HVAC/R system life.
GulfCoat® Product Offering
GulfCoat® | Corrosion Coating | to protect coils and system components, select Aerosol for small applications and Sprayed Applied for larger systems – both available in Blue, Clear or Gold. |
GulfCoat® | AM- Antimicrobial | a silver ion coating to inhibit mold, mildew, and bacteria growth, especially on evaporator coils to improve indoor air quality. |
GulfCoat® | Circuit Shield™ | to protect printed circuit boards and connectors from corrosion causing moister and add a high dielectric protection layer to mitigate short circuits or erratic operation caused by common vermin like geckos, snakes, insects, and anything else that can climb on a system’s circuit board. |
Corrosion coating is available in Blue, Clear or Gold